“Oh, that’s a fun failure mode!” I was talking with a friend of mine recently, and they were talking about a technical problem they were solving[1], specifically about the failure mode that they had seen, and before they could explain their solution, I made the exclamation above.
Failure modes have always fascinated me. I don’t know if that’s a cause of or a result of[2] me going to engineering school[3]. I remember being fascinated (and appalled) by the video and story of ‘Galloping Gertie‘. The torsional twist as a reaction to wind and subsequent failure mode[4] is an image I’ll never forget.
Our undergrad bridge-building course professor[5] seemed to also be very interested in giving us images and experiences of materials actually failing. My favourite was his demontration of the failure characteristics of steel cable. In class, he showed us a diagram similar to this one:
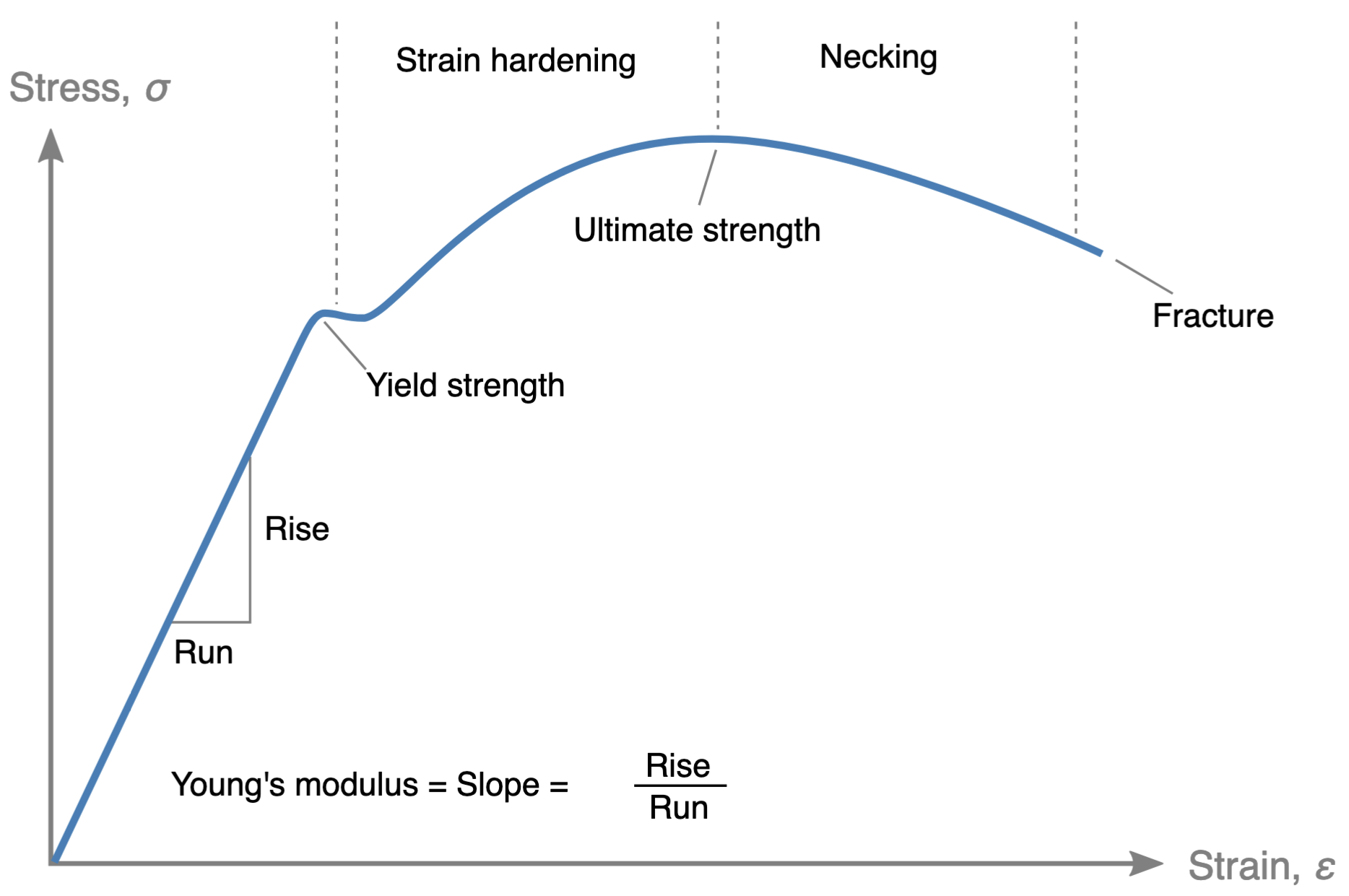
Source: Wikipedia user Nicoguaro
Notable parts of this stress-strain diagram include but are not limited to:
– The ‘elastic region’, amounts of stress/force/pressure where the material will stretch but return to its original shape and size[6]
– The ‘strain hardening region’, where the material will adjust and become somewhat stronger. (This may be undesirable)
– The ‘necking region’, where the metal/material starts to lose strength because the atoms can no longer fill in the gaps, causing narrowing of the cross-section (the ‘necking’), eventually leading to fracture, where the material fails
The demonstration included measurements of the deformation of the steel, using a precise length measuring device[7] to provide numerical measurements. Such a device is required, because the deformations we’re talking about are tiny, due to the large Young’s Modulus of steel.
Another demonstration was using a jug of water to break a wooden dowel. The dowel was fixed to a desk, with one end extending (cantilever-style), where the jug was hung at various points. This was intended to show how the torque[8] (of the mass of the hanging water times the distance from the cantilever point) would increase the force, leading to eventual failure of the dowel.
At least that was the intended demonstration. The dowel was so flexible that it bent downwards far enough to minimize the amount of torque/force, preventing it from breaking. So instead, we got to see a failure mode of the intended failure mode instead (and learned something about the resilience of trees!).
Perhaps most memorable was witnessing a failure mode of the professor, who, discontented with his dowel not failing in the experiment, broke it himself over his knee, showing us both the actual failure mode of wooden dowels and how frustration and anger can contribute to engineering failures.
For a great explanation of the different failure modes of different types of materials, especially what it is that makes wood so resilient, I recommend the textbook we used in this course:
Both of these demonstrations left strong impressions on me. I still remember them more than 25 years later (and I suspect many of my classmates do as well).
Given how visceral and effective these demonstrations were, it would make sense to work out a (reasonably) full set of reasons that engineering[9] projects fail, and create demonstrations and labs based on those, so that the students have those visceral memories to call upon, to warn and inform them.
But what is that set of reasons that engineering projects fail? How do you categorize and teach failure modes systematically?
That’s a question for next time! (Spoiler alert, it will probably involve the ‘swiss-cheese model‘.)
[1] It was a type of problem that I had designed a system to avoid in the past, so it was kind of cool to see an instance of it ‘in the wild’, so to speak.
[2] Or both!
[3] Or growing up with a parent as an engineer
[4] And the poor dog!
[5] Thanks, Prof. Collins!
[6] For those who have been following the news recently, this is one of the reasons that steel is used for pressure vessels such as submarines.
[7] I was originally going to suggest that this was some sort of strain gauge, but if my memory serves me correctly, I remember a dial moving showing deformation. If anyone knows the type of device typically used for such a test, please comment below!
[8] This may have also been the lesson where I learned the second meaning of the phrase ‘Every Couple has its moment‘.
[9] I’m using the word ‘engineering’ here because all of the demos I talked about were related to mechanical engineering/bridge building, but much of this will apply to software engineering as well.
Links to image on Wikimedia Commons, Creative Commons license available there:
Stress/strain curve
S’s note to me, to help me write this post: “Please pick two failure modes and write about them! Then you can add a bonus failure mode, which was you getting overwhelmed by the number of possible failure modes and timing out before writing anything. “